The Future of Modern Methods of Construction (MMC) and the Creation of Sustainable Communities
February 5, 2024
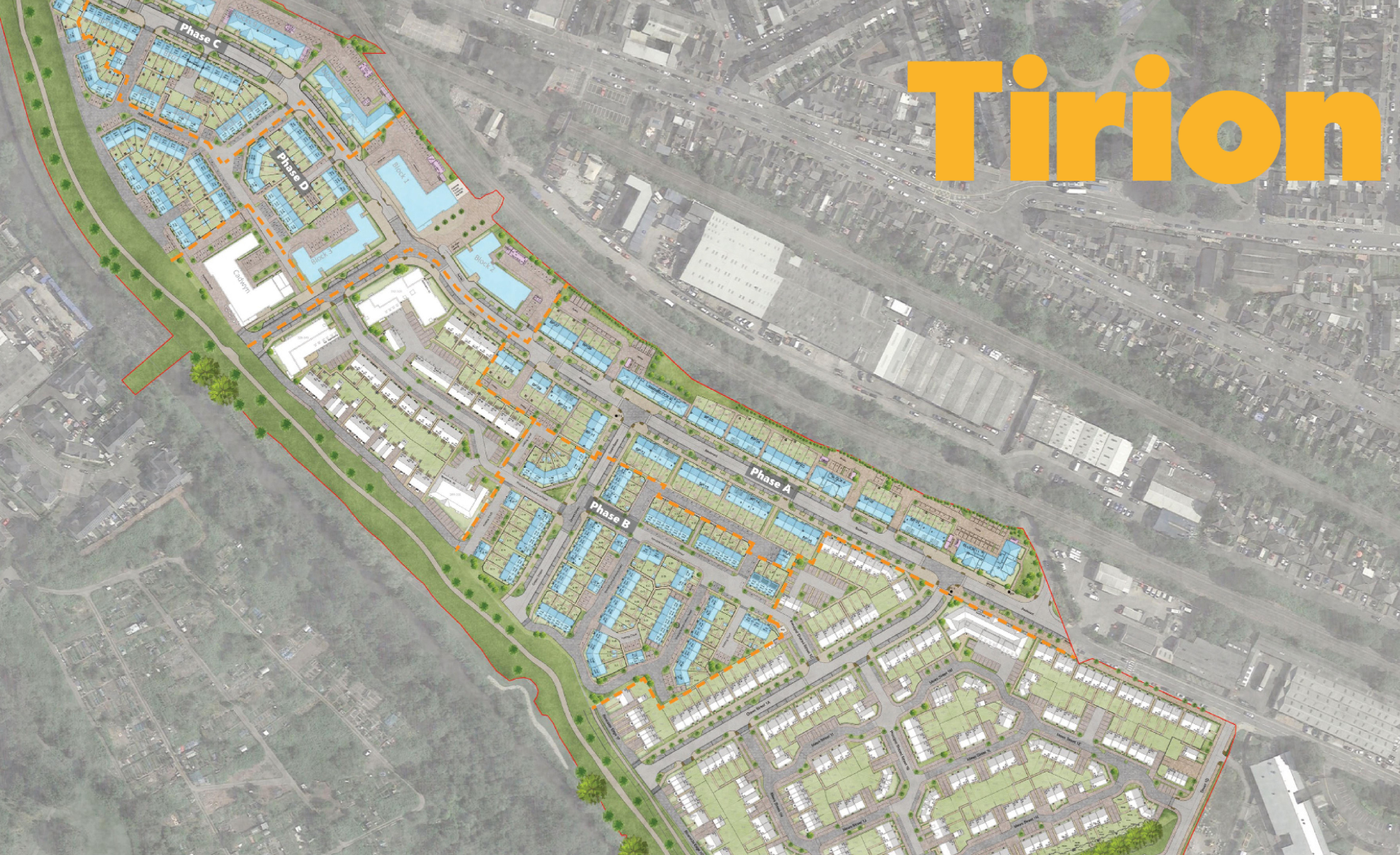
The housing crisis in the UK is well documented. The Welsh Government is looking to build 20,000 affordable homes by the end of the Senedd term in 2026. Alongside the basic requirement for more homes, there is a drive to improve space standards, energy performance and placemaking to create sustainable communities.
These ambitions are currently constrained by a financial crisis which inevitably requires an increased focus on economy, and best value solutions. This is driving Tirion to continually review and explore modern methods of construction (MMC), to improve qualitative and quantitative outcomes at a faster pace and lower cost.
Key to this process is understanding why various MMC initiatives have underachieved and how the obstacles they have encountered may be overcome. Despite the potential benefits, MMC has been slow to take off. A recent report showed that the proportion of new homes built using MMC was currently only between 6 and 10%.
Nevertheless, prior to recent adversity, adoption of Off-Site Manufacturing (OSM) was growing in the housing market. Various degrees of factory manufacture are used including flat wall panels (some including windows), bathroom pods, kitchens, stairs, roof dormers and fitted out volumetric housing units. Quality benefits have been delivered but factors inhibiting success include high costs, constrained flexibility, and perception of poor aesthetics. With the wisdom of hindsight, the failure of the volumetric businesses (whole rooms or complete homes) to compete in the general residential market was somewhat predictable.
The benefits of MMC have yet to be fully realised and much work needs to be done in terms of optimising design, construction, OSM processes, client education, and supply chain interrelationships. However, if the obstacles can be overcome, MMC has the potential to deliver:
- Better quality and more durable homes, requiring less maintenance.
- More homes, built faster, for less cost.
- Lower energy and carbon consumption during manufacture, as well as construction and the building’s lifespan.
- Less material consumption and less site waste.
- Improved health and safety.
- Sustainable skilled employment opportunities.
- Guaranteed volumes to enable funding of factory set-up costs and automation.
- Standardisation of house designs and components.
- Acceptance of manufacturer leadership of design and construction.
- Positive attitudes from insurance organisations and mortgage companies.
- Positive assistance from planning and other statutory authorities.
- Creative ways of delivering appealing place-making and customer aspirations.
- The way 85% of us feel is influenced by the architecture that surrounds us and the places in which we live.
- 81% of people take an active interest in how buildings both look and feel (Streets of Shame, 2002, CABE Commission for Architecture and the Built Environment).